Yale scientists uncover deformation mechanism of metallic glass at the nanoscale
The research includes insights into how metallic glass deforms on a nanoscale lay the groundwork for constructing better materials.
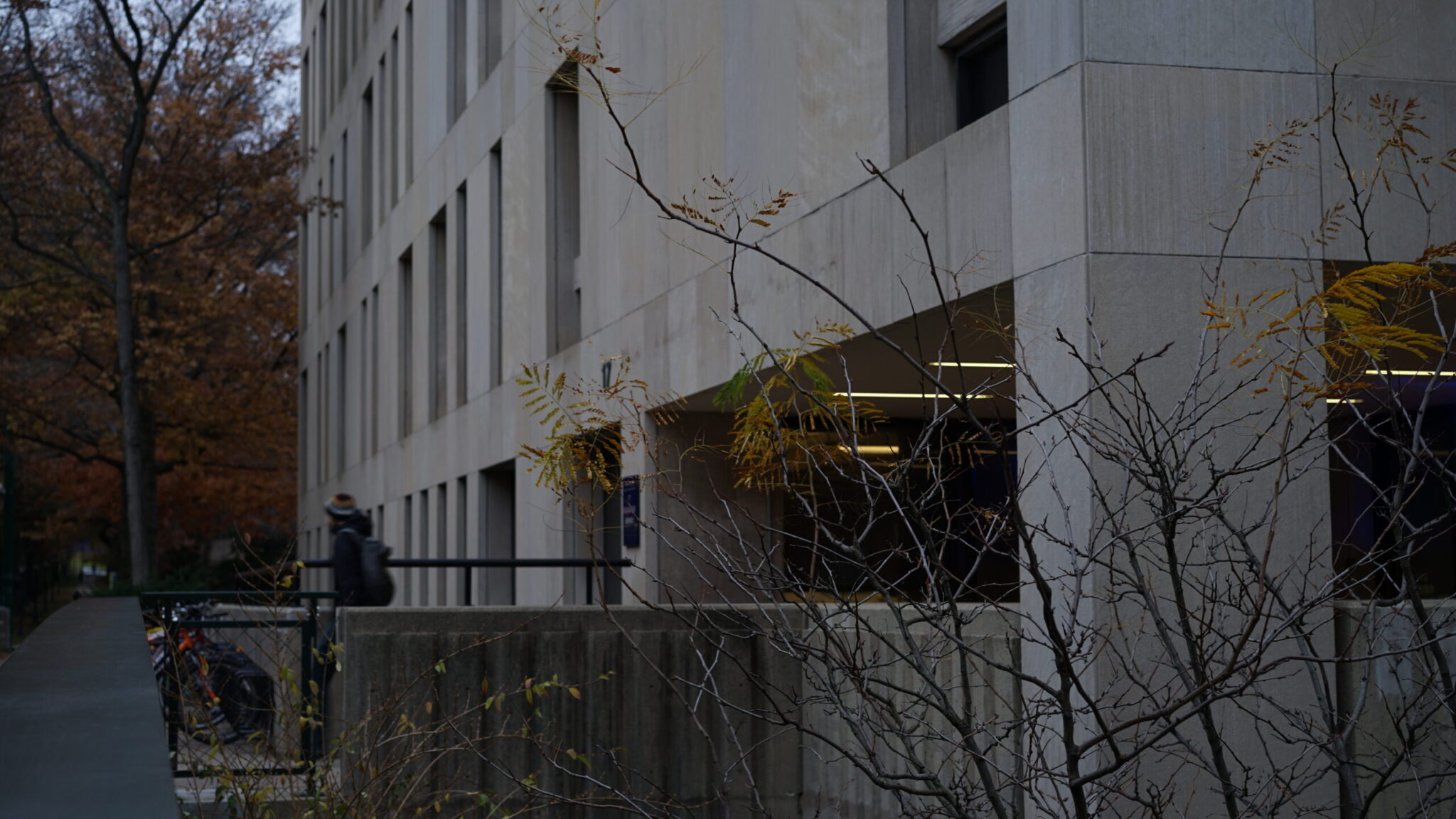
Ling Gao
Yale researchers have found a novel mechanism of how metallic glass deforms at a nanometer scale.
Jan Schroers, a professor of mechanical engineering and materials science, and Naijia Liu, a former doctoral student in the lab, along with other researchers, studied the mechanical properties of metallic glass by molding nano-size features on the samples. In metallic glass, or amorphous metal, atoms are arranged randomly. When heated enough, metallic glass softens to a viscous, liquid-like state, like honey. By examining how the material deforms at different nanometer scales, the researchers proposed that metallic glass deforms at lower temperatures and smaller sizes by atoms diffusing individually rather than flowing as a group.
According to Liu, while researchers have demonstrated that other materials, such as crystalline metals or semiconductors, can deform by atomic diffusion, they have not shown that amorphous materials could do the same.
“In the case of amorphous material, especially amorphous metals, for the entire community, no people before had confirmed that these amorphous materials can deform through diffusion,” Liu told the News. “So, scientifically, this is a new thing.”
Liu said that one can divide materials into two categories: ordered or disordered, or, in the terminology of material science, crystalline or amorphous. While many researchers have analyzed the structure and properties of crystalline materials, they know much less about amorphous materials, including their structural properties and how they deform, according to Liu.
Though crystalline materials may seem to have perfectly ordered and predictable structure, they often contain defects due to misaligned atoms and boundaries between smaller crystalline grains. According to Sungwoo Sohn, a co-author of the study and an associate research scientist in the Department of Mechanical Engineering and Materials Science, these irregularities, even if small, can cause concentrated stress and material breakage.
“So what is a perfect thing?” Sohn rhetorically asked. “It can be a single crystalline, so everything [is] in order. Or it can be imperfectly perfect. So everywhere is random [and] there is no order … That is also perfect in another way.”
The randomness in amorphous material — its “imperfection” — allows stress to spread out more evenly, making it less brittle and more malleable. Similar to other amorphous materials, like plastics or glass, researchers can use a mold to shape it. In this way, amorphous metals combine the properties of metal and plastic, having both strength and flexibility.
Molding can happen with nanometer precision. In this study, the researchers used a mold with an array of nanometer pipes, whose diameter ranged from 10 nm to 250 nm, and experimented with different four-element alloys. Then, they pushed the samples into the mold, generating tiny whisks on its surface. They expected the wires to get shorter as the diameter of the holes got smaller, suggesting that the material collectively flowed into the pipes.
“People have a concept of collective movement. It is like a viscous fluid,” Sohn said. “Let’s say you squeeze the ice cream. We don’t expect the ice cream molecules are going to jump one by one. They just [are] collectively pushed away, pushed inside. So that’s how people have imagined.”
However, at lower temperatures and smaller hole sizes, the behavior of the materials deviated from the collective movement. When the researchers used a small enough hole, the wires became longer. According to Liu, this relationship between size and length helped distinguish different deformation mechanisms. In collective flow, the length of the nanowire is positively correlated with size, but the length of the nanowire is inversely correlated to the root square of size in diffusion.
After examining the data, the researchers proposed that under these conditions, the atoms in the amorphous metal move as individuals through diffusion instead of flowing as a collective. This mathematical model explained the size-length relationship and the variations they observed in nanowire compositions.
According to Corey O’Hern, a professor of mechanical engineering and material science, this study helps fill the research gap on metallic glasses at small scales.
“For the past 50 years, the field has characterized the mechanical properties of metallic glasses on meso- to macroscopic scales above 100 nm,” O’Hern wrote in an email to the News. “But the field has made little progress on visualizing and understanding the atomic motion in response to applied deformations on lengthscales below 100 nm.”
O’Hern also noted that understanding the atomic behavior of the material enables researchers to manipulate and predict its behaviors. For example, when amorphous materials are under stress shear bands — dislocations within the material — can appear. But the location of these shear bands remains unpredictable, O’Hern told the News, and this study is an important first step to understanding this phenomenon.
Further, studying how a material deforms could also lead to the generation of better materials. As Liu pointed out, if a material is built by diffusion, the atoms can find more optimal positions instead of staying in their predetermined arrangements and form a more stable structure. For Liu, this mechanism could inform researchers seeking to achieve the synthesis of ultra-stable amorphous materials.
“In the basic science point of view, the unknown part is the part that we want to work on — to fill the unknown cavity,” Liu said. “That’s why I think amorphous study is very, very interesting.”
The first reported glass metal was produced in 1960.